separator-02 水素技術で未来を拓く、時代の最前線となる金属セパレータ順送金型の開発
世界的な水素社会への動き
水素社会に向けた世界の取り組み
ウクライナ侵攻を契機に、エネルギー構造の変革が世界的に加速し、水素社会への移行に向けた動きも加速しています。
ドイツでは、水素導入目標が当初の2倍となる2030年までに10GWに引き上げられました。米国のインフレ抑制法(IRA)や各国における化石燃料との価格差縮小支援策なども推進されており、大規模水素製造プラントの建設計画も相次いで発表されています。 具体的には各国は以下のような取り組みを進めています。
- 支援策の充実
米国:インフレ抑制法(IRA)
各国:化石燃料との価格差縮小支援策 - 大規模水素製造プラントの建設
サウジアラビア:世界最大規模のプラント建設
豪州:大規模グリーン水素プロジェクト
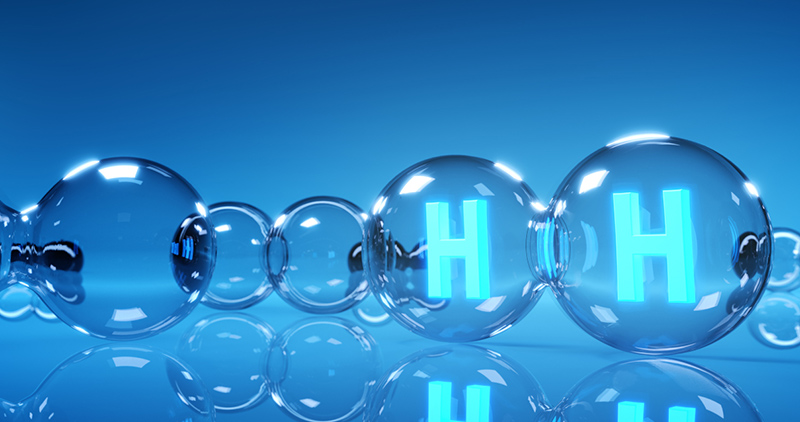
日本もこの流れを受け、2023年6月に水素基本戦略を6年ぶりに改定しました。
2040年までに水素等の導入目標を1,200万トンと新たに設定し、2030年までに国内外で水電解装置15GWの導入目標を掲げました。
日本は、水素技術において世界をリードする存在であり、今後も積極的に取り組んでいくことで、水素社会の実現に大きく貢献していくことが期待されます。
水素社会実装へ、大きく立ちはだかるコストへの壁
1. 燃料電池製造コスト
1つ目として燃料電池の製造コストが高いことです。
燃料電池には触媒や電極に高価な材料が使われており、それらが数百枚と積層されるため装置全体が高額なものになります。
2. 水素供給コスト
現状の水素供給コストは、一般的に1Nm3あたり100円~150円程度となり、計算するとガソリンより高くなってしまい社会実装は普及が思うように進みません。
順送金型による燃料電池金属セパレータのコスト低減
1. 高効率生産と高品質管理
燃料電池は、高効率かつ高品質な生産技術の開発が不可欠です。従来の生産方法では、これを実現するために膨大な設備投資とスペースが必要となります。
→今回開発した順送金型により、金属セパレータ製造の設備コスト圧縮や省スペース化が期待されます。
2. 材料ロスの低減
燃料電池の製造には、高価な材料を多く使用するため、材料ロスの低減が重要です。
→今回開発した順送金型は材料ロスを極力抑えるレイアウトにすることで材料コストの低減に期待されます。
3. 原料・プロセスの低コスト化
燃料電池のコスト低減には、原料や製造プロセスのコスト削減が不可欠です。セパレータの金属化による大幅なコスト低減と高生産性が期待されています。
→今回開発した順送金型は、金属セパレータをハイスピードで大量生産が可能となり、1枚当たりの製造コストを抑えることが期待されます。
4. 金型耐久性の向上によるコスト低減
金属セパレータは耐食性が高い材料を使用するため、加工難易度は増加します。コストを削減するためには金型の寿命向上も大きく求められます。
→今回開発した順送金型は、1μmオーダーの高精度金型部品の位置決め・クリアランス調整を行うことで金型の寿命向上が期待されます。
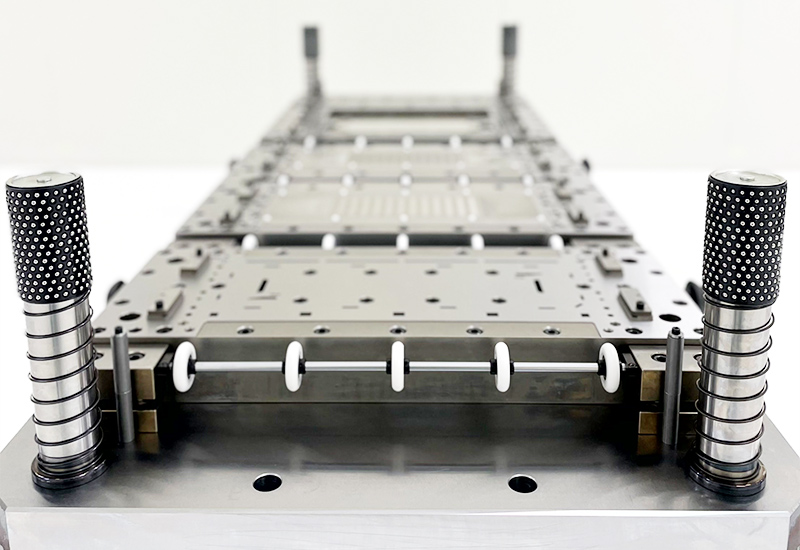

サイベックコーポレーションの新しい挑戦
弊社のCFP(Cold Forging Progressive)工法を活かし、金属セパレータ向け冷間鍛造順送金型の開発を行い、高効率生産による金属セパレータの低コスト化へチャレンジしております。
目標とする生産スピード
1分間の生産枚数
従来の生産ライン 6枚/分
目標の生産ライン 60枚/分
生産スピード10倍の向上を目指します。
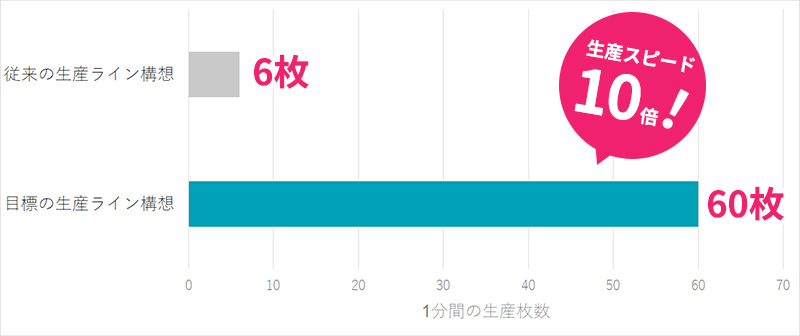
従来の生産ライン構想
ブランクを投入装置にセットし、ロボット等の搬送装置を用いて、各工程を搬送します。プレス機と搬送装置を連動させ各プレス機の冷間鍛造金型(単型)にて生産する方法です。

※製品形状等でプレス工程数は変動致します。
目指す生産ライン構想
材料はコイル材をダイレクトに投入し、金型内を送り装置で搬送します。使用する金型は冷間鍛造順送金型を使用。弊社のCFP(Cold Forging Progressive)工法を採用した生産方法です。

冷間鍛造順送金型のメリット
1. 設備投資額の削減
冷間鍛造順送金型になる事で、複数のプレス機、それを繋ぐ搬送装置が必要なくなり全体の設備投資額を圧縮できます。
2. 生産ラインの省スペース化
複数のプレス機、それを繋ぐ搬送装置が必要がなくなることにより、生産ラインがコンパクトになり、省スペース化を実現します。
3. 生産スピード向上
搬送装置のタイムロスがなくなり、プレス機の加工スピードに追従できる生産スピードを実現します。
今回開発中の冷間鍛造順送金型での製品サイズ
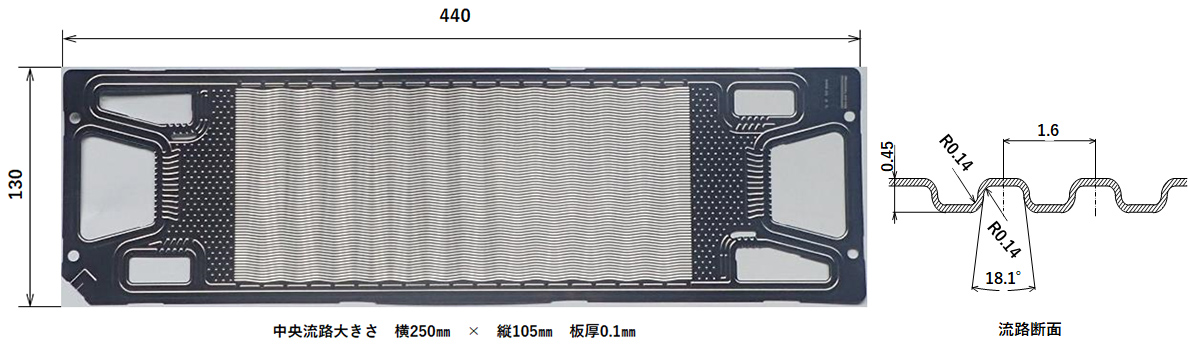
金属セパレータ順送金型動画
カーボンニュートラルに向けた燃料電池用金属セパレータ技術開発
半導体・情報伝達技術の未来
半導体と情報伝達技術の未来は、半導体の微細化限界に直面しながらも、積層化や3D実装、異なる種類のプロセッサを組み合わせることで、全体的なコンピューティング性能を向上させるなどの新たな進化を遂げています。5GやAIなどのデジタル技術の発展により情報伝達技術が進化し、自動走行やFA( factory automation )、スマートシティなどの新たなアプリケーションシステム・デジタルユースケースが増えています。デジタル化の推進、新しい製品・サービスの創出、そして社会課題の解決に向けた取り組みが進められています。これらの進化と取り組みは、半導体と情報伝達技術の未来に大きな影響を与えていくことになります。
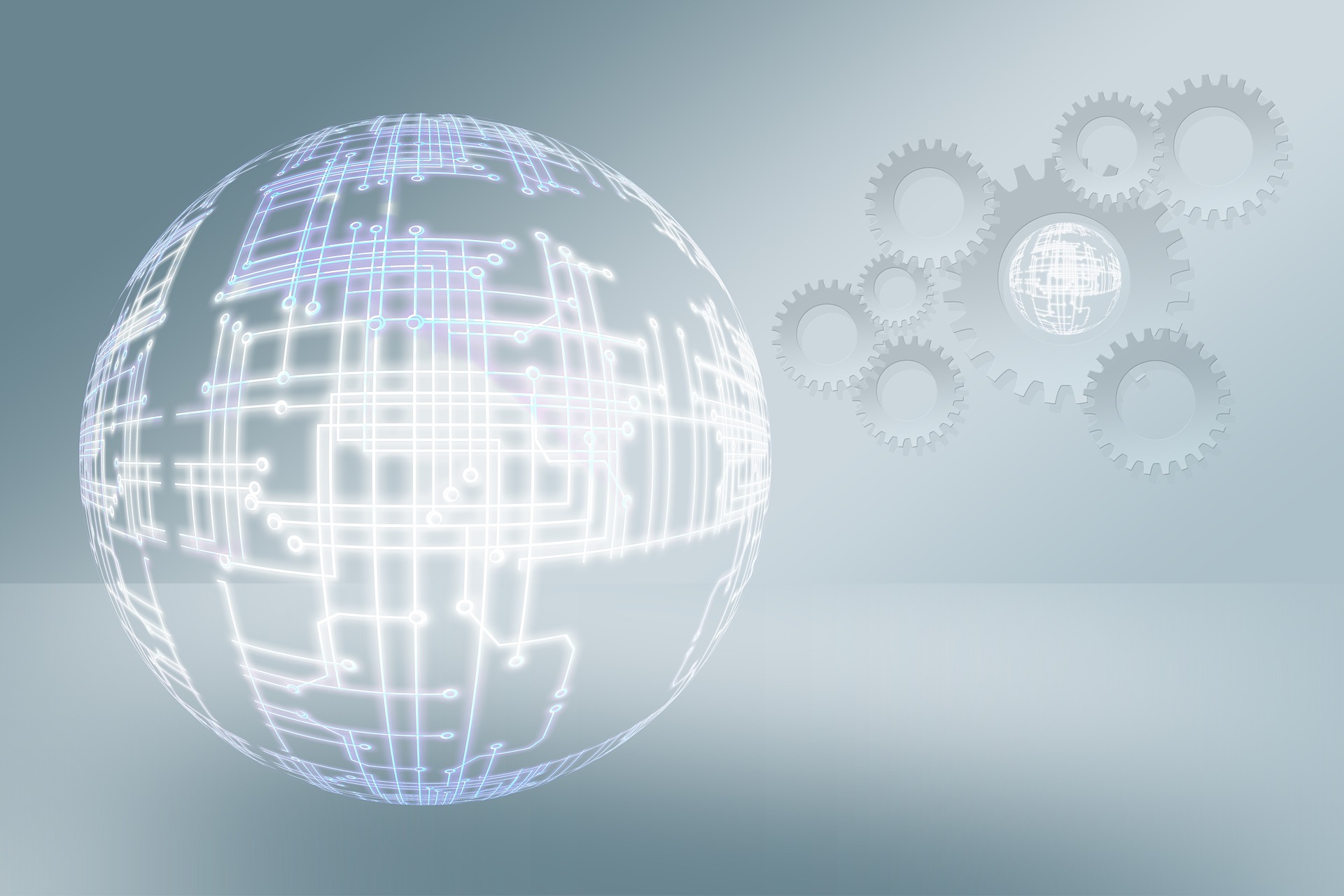
次世代半導体部品に求められるもの
半導体関連部品は
- 電子機器の性能向上
- 電気自動車の普及
- サーバーやデータセンターの増加
- 半導体製造の拡大
といった大きな環境変化と共に今後も著しく成長していきます。
半導体市場が拡大する一方で、半導体自体を高効率で冷却する技術が課題となっております。電子機器は、小型化・高性能化が進むにつれて、発熱量も増加します。その為、ヒートシンク部品は、今まで以上に高効率で電子部品を冷却することが欠かせないものとなっています。
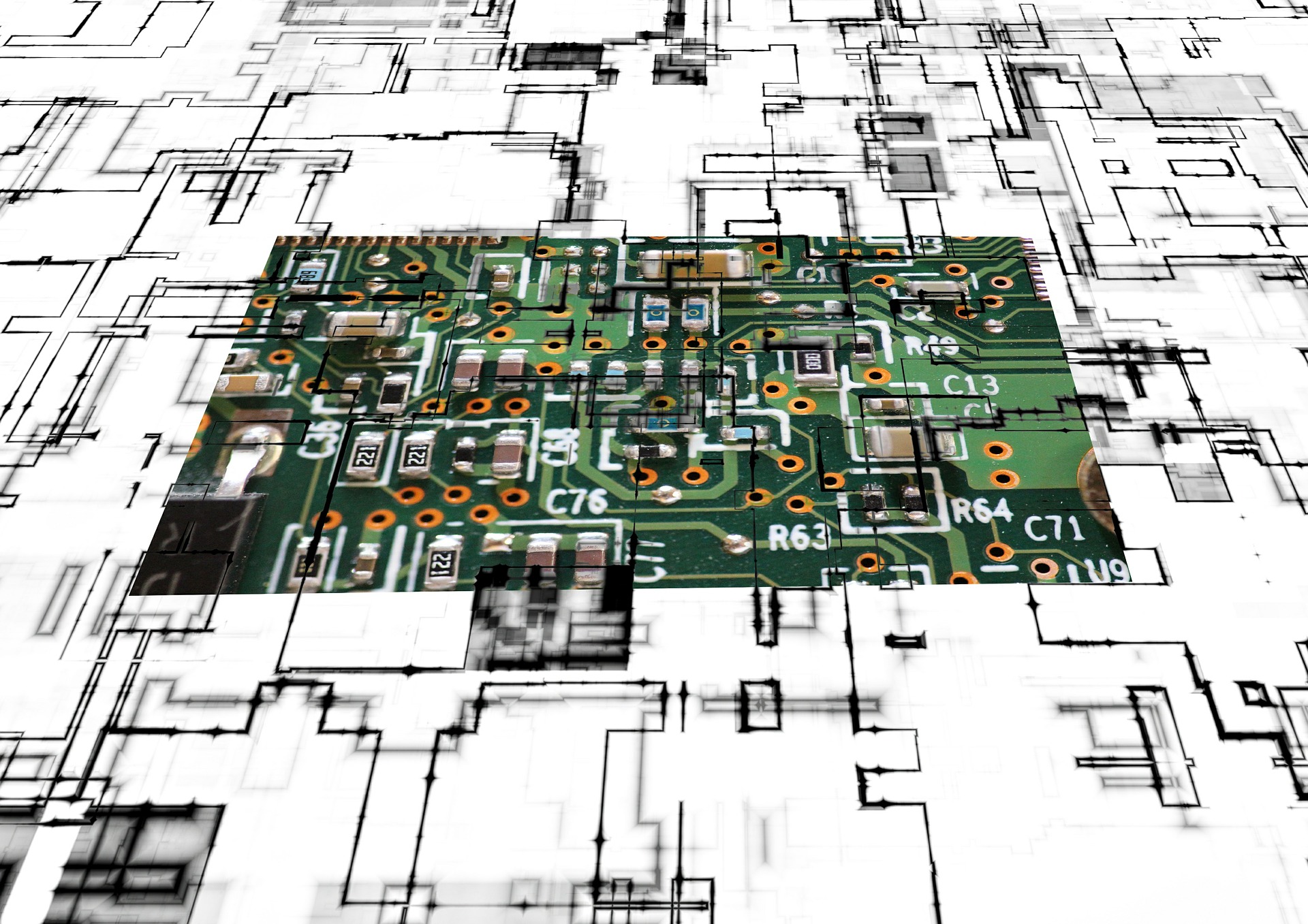
ヒートシンク・ヒートスプレッダの技術開発
軽量で高効率な熱マネジメント部品の需要は今後も益々増加していくと予想され、アルミや銅といった非鉄材のCFP (Cold Forging Progressive )技術開発を進めております。
CFP (Cold Forging Progressive )技術は冷間鍛造を含める加工方法なので、高い精度、複雑で微細な形状で加工することができ、機械的性質・強度を高めることができます。
更に順送プレスにて、一度に多くの部品を安定した品質で生産することができ、大量生産に適しています。
主に手掛けている製品は今後数量が見込まれる部品2点となります。
ヒートスプレッダ:電子機器や家電製品などの内部で発生する熱を効率よく伝達するための部品 (材質:アルミ・銅)
ヒートシンク:熱を空気中に放散するための部品 (材質:アルミ・銅)
CFP(Cold Forging Progressive )技術を活用し、 微細鍛造・高精度成形・各素材への対応など新しい技術開発を進めております。
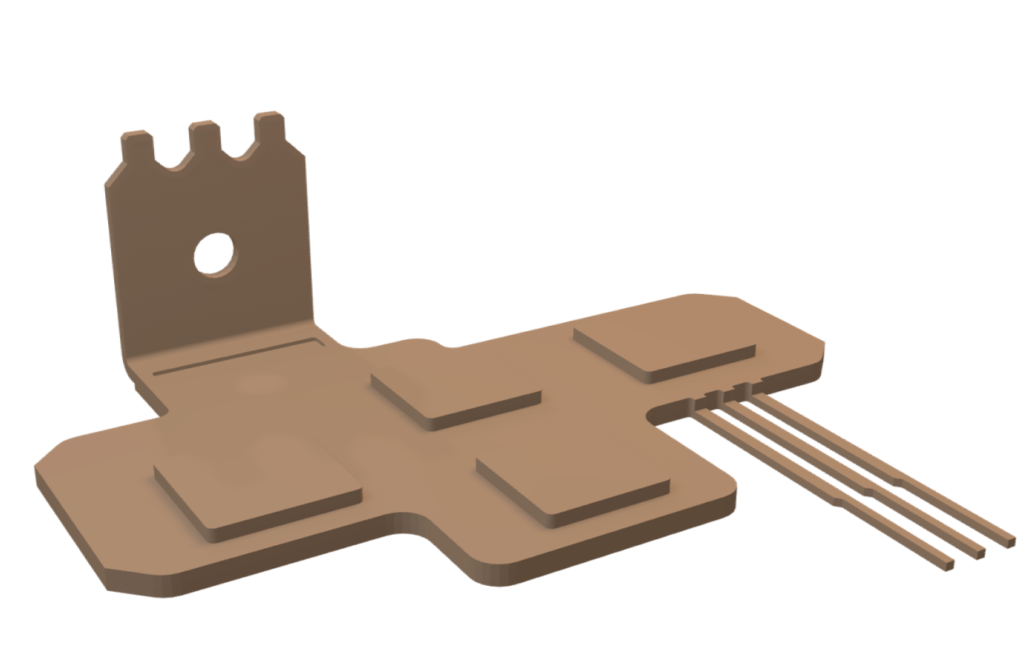
アルミ・銅のプレス成形性課題
アルミ・銅材によるプレス加工は、成形性の問題を抱えています。
延性は軟鋼板に比べて低く、しわや割れなどが発生しやすく、また流動性が良く微細な形状の確保が困難です。
その中で性能特性を向上するために製品の要求項目としては以下のようなものがあります。
- チップや素子設置面側の凹凸形状は崩れず(ダレ・ヒケ無く)に高精度に微細成形が必要。凹凸精度10~50μm。
- 製品裏面は熱を伝えるため平滑な面が必要。平面度0.1㎜以下。
技術開発報告
- 平面からの一体化成形によりプレスのみで完結され、後工程の切削工程や接合工程が不要となりました。
- アルミ材について凹凸形状は崩れず(ダレ・ヒケ無く)に微細成形に成功しました。
- アルミ材については平面度0.1㎜以下をクリアしました。
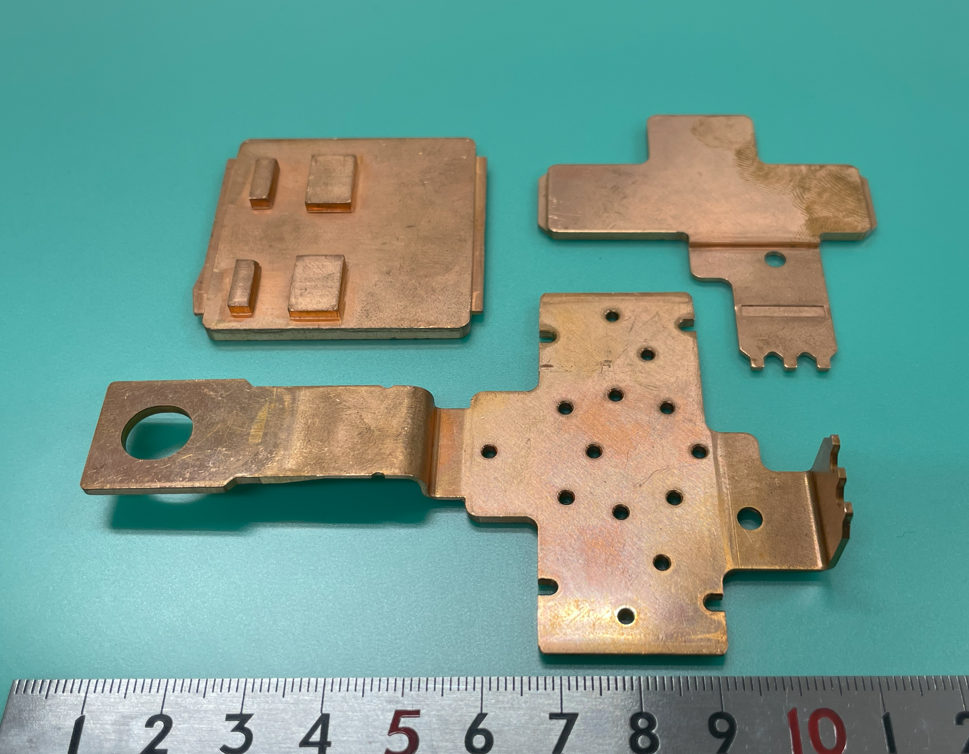
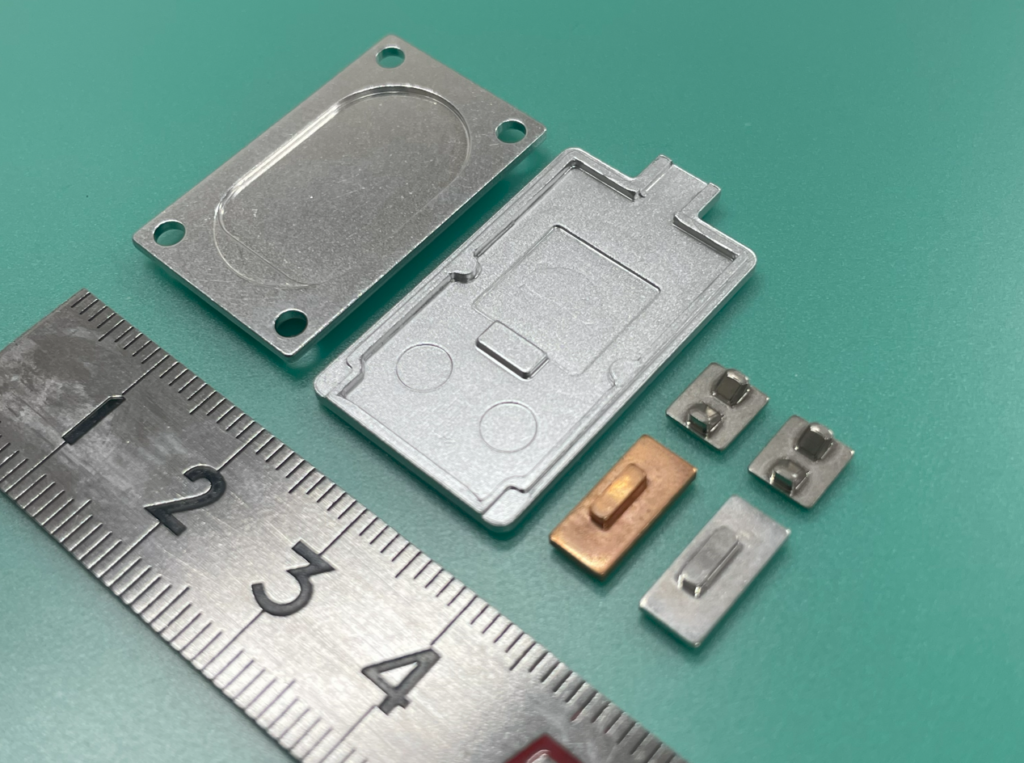
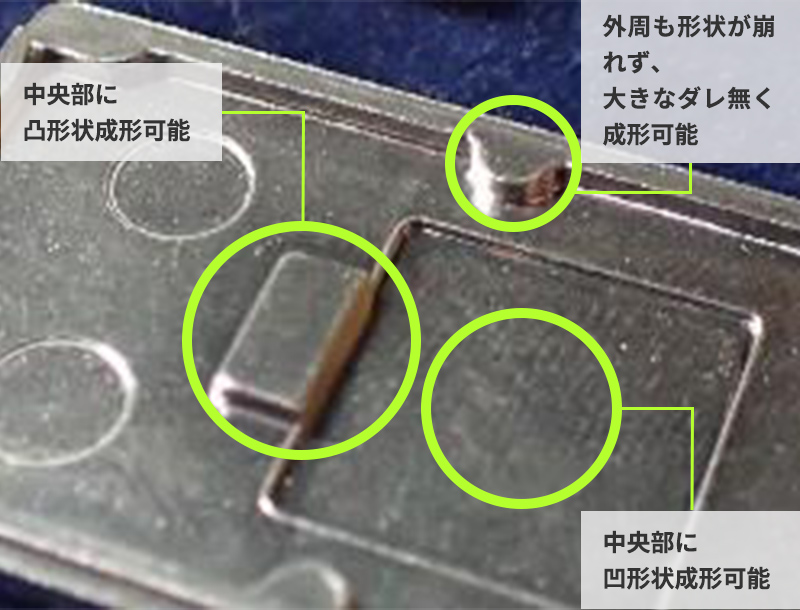
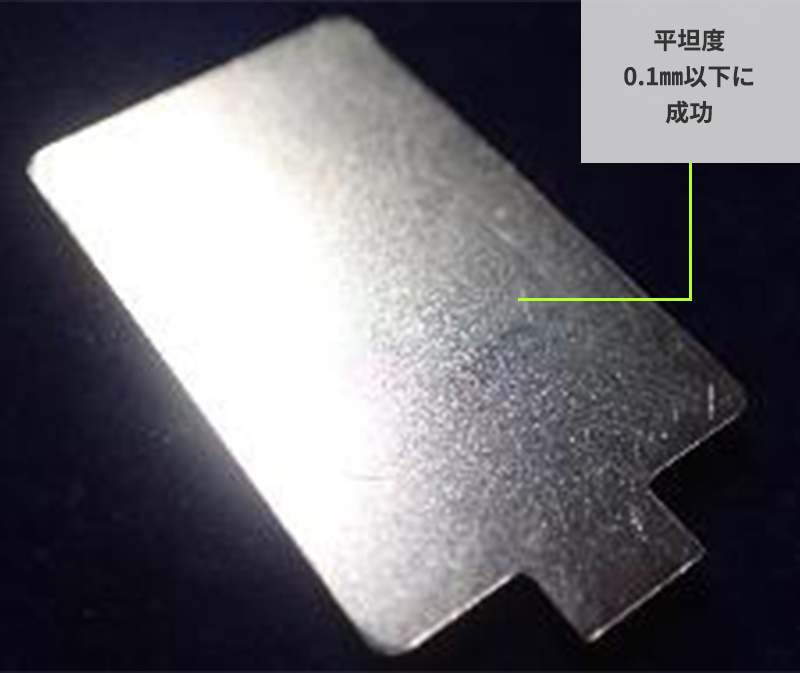
更なる課題へのアプローチ
ヒートシンク・ヒートスプレッダ製品の更なる性能向上を求め、平面度に対して現状以上に向上を図っていきます。
微細偏肉の細かい凹凸部分の形状精度の向上を図っていきます。
CAE(解析ソフト)活用
アルミ・銅の板鍛造の技術開発にあたり、解析ソフトを利用して素材の流れを確認しながら工程設計や金型部品の形状の検討を行い、より精密で正確性の高い技術開発を進めております。
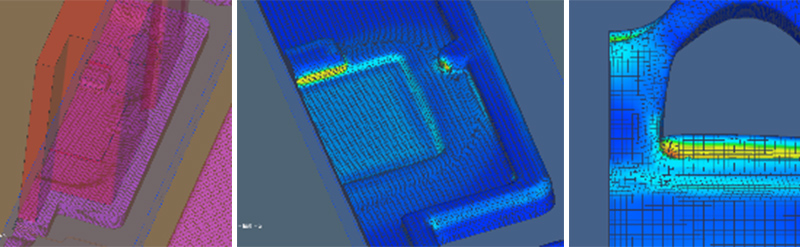
カーボンニュートラルのハブとなる燃料電池
燃料電池は、水素と酸素の化学反応によって電気と水を生成する発電装置です。化石燃料に比べて環境負荷が少なく、再生可能エネルギーと組み合わせることで、持続可能なエネルギー源としての役割を拡大することが期待されています。こうした技術革新の進展により、燃料電池は、自動車を始め発電設備、家庭用燃料電池など、さまざまな分野で活用されるようになってきており、これからのカーボンニュートラル社会のハブとなる役割を担っております。
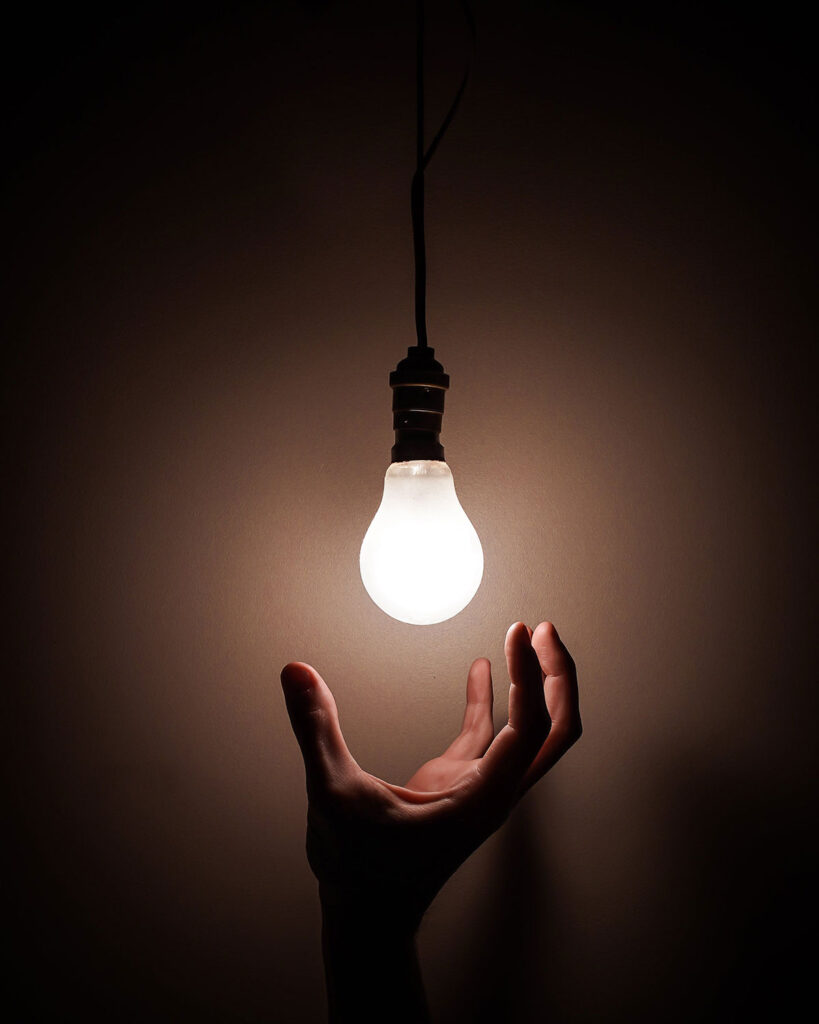
金属セパレータへの技術開発と取組み
サイベックコーポレーションは2004年より金属セパレータの金型製作・プレス加工の技術開発がスタートし、現在に至るまでに計51件の案件に取り組んでいます。各社大手自動車メーカーとともに金属セパレータの設計段階からプレス成形性の評価し、多種にわたり、金属セパレータの試作開発を行ってきました。サイベックコーポレーションを選んで頂ける理由として、①地下工場で製作する超高精度金型、②共同開発した高剛性プレス機により、高精度な金属セパレータのプレス加工を実現できることです。金属セパレータの材質はステンレス・アルミニウム・チタンを主に板厚0.08~0.2mmの金属セパレータのプレス加工実績があります。また、 最近ではこの先将来を見据えた大判サイズの金属セパレータ順送プレス加工技術の開発に取り組んでいます。プレス加工後の後工程も考慮し、お客様の要望に合わせた製造ラインのご提案をいたします。
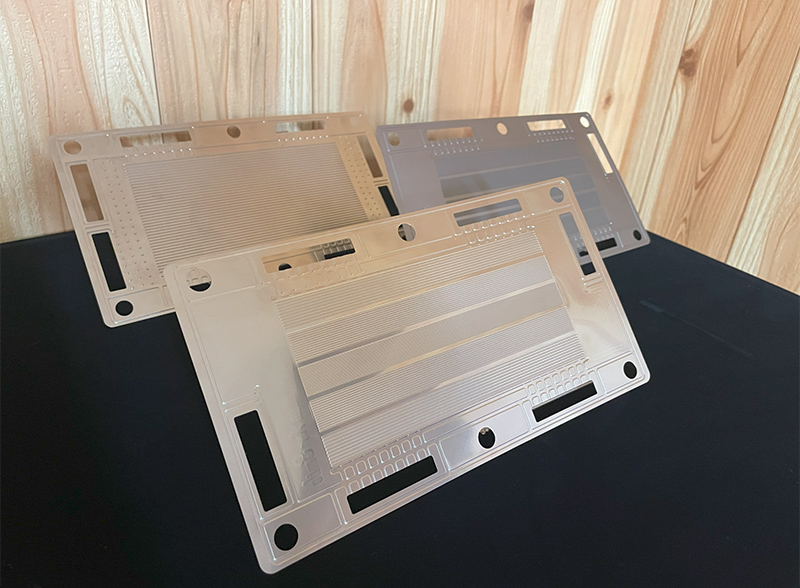
金属セパレータの試作実績
2004年~2022年 50案件の試作受注
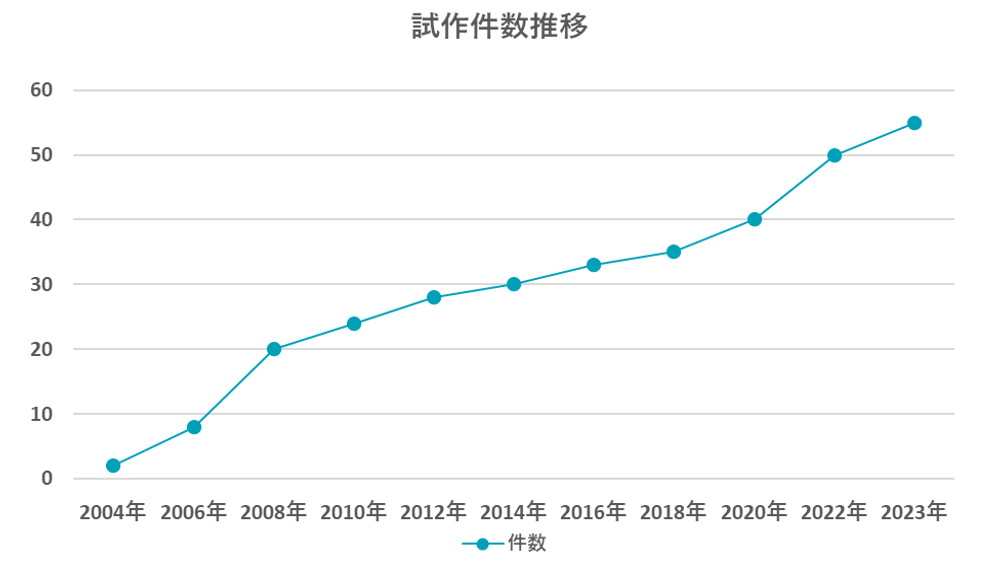
直近3年の試作案件実績
2021年度
5件
2022年度
5件
2023年度
5件
素材
金属セパレータは、燃料電池の主要部品です。従来はカーボン製セパレータが使用されていました。しかし、近年では、低コスト化、コンパクト化、耐衝撃性などの観点から金属セパレータが注目されています。 金属セパレータの材料としては、ステンレス、アルミニウム、チタンなどが主流です。特に、今後ステンレス鋼は最も期待されている材料の一つです。
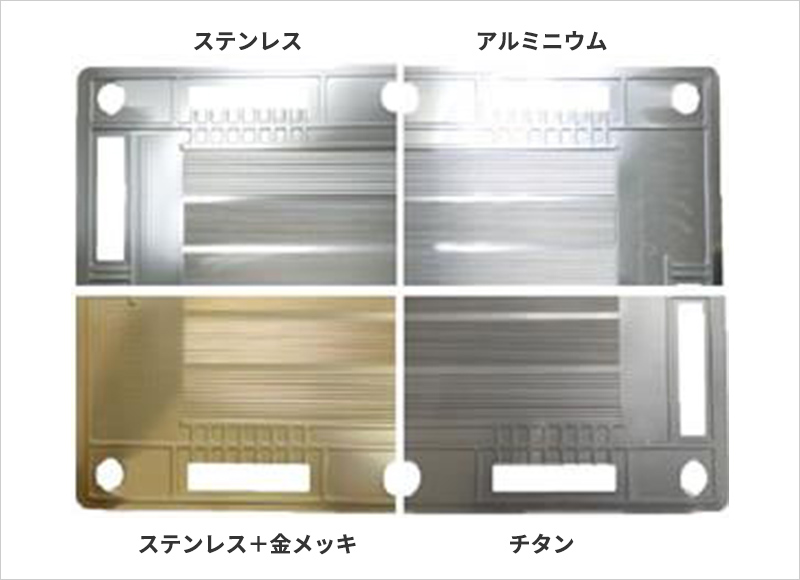
サイズ
技術開発した金属セパレータは手のひらサイズ(JARI規格)から大判サイズまでの実績があります。
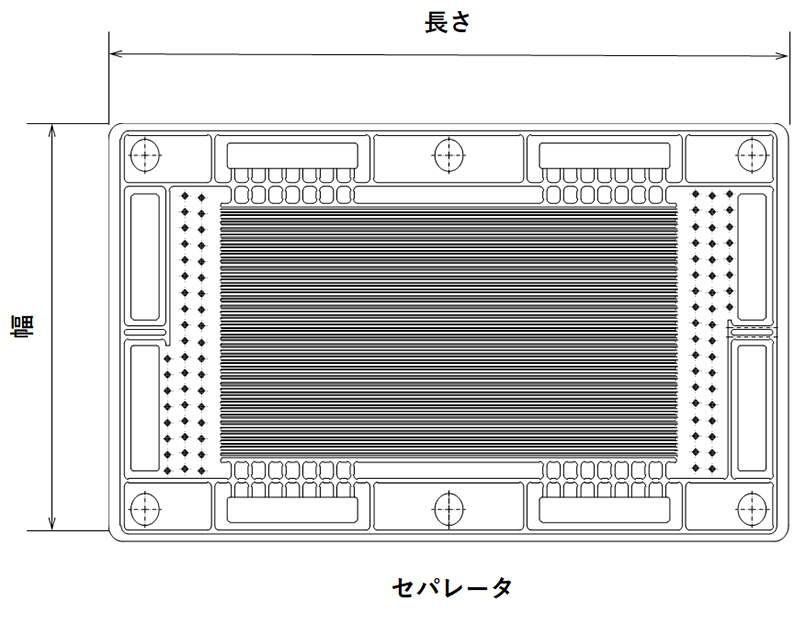
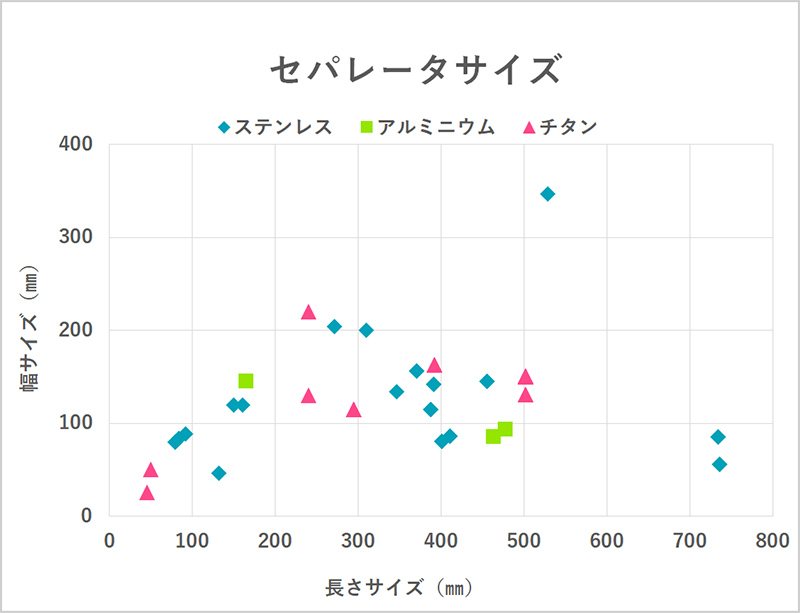
製品最小面積実績 | 1,196mm2 |
製品最大面積実績 | 18,356mm2 |
※流路形状、成形面積、材質・板厚等により成形可能限界範囲は異なります。
流路形状
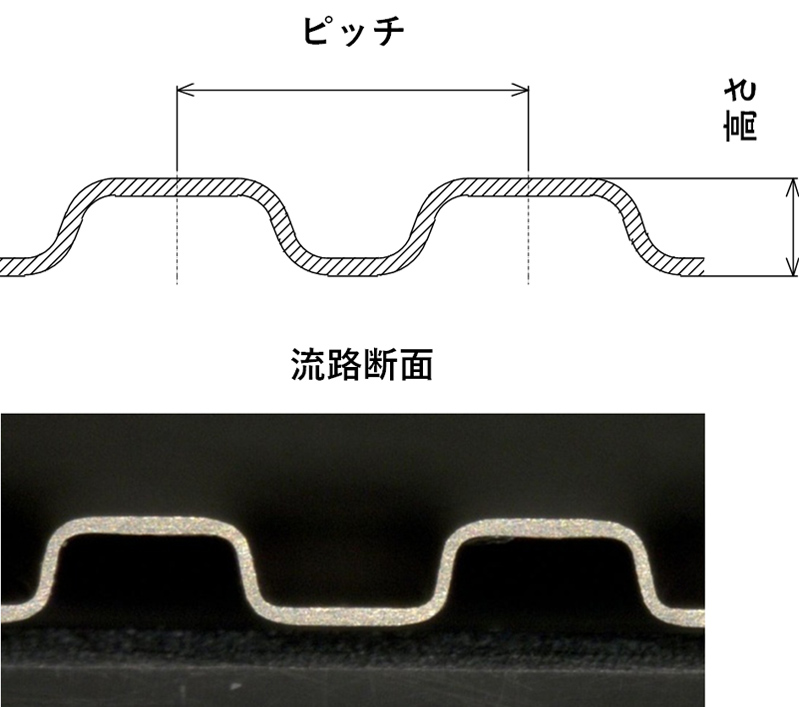
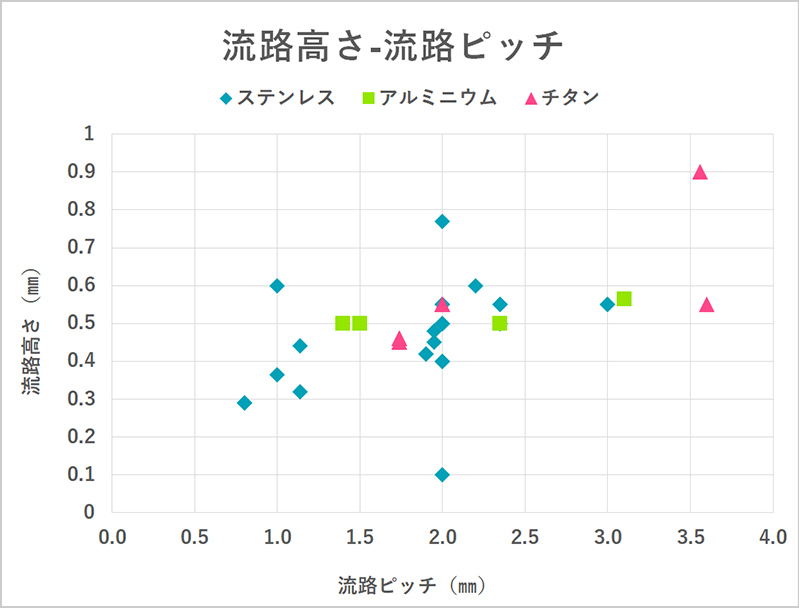
流路最小ピッチ実績 | 0.6mm |
流路最大ピッチ実績 | 3.6mm |
流路高さ最小実績 | 0.1mm |
流路高さ最大実績 | 0.9mm |
※流路形状、成形面積、材質等により成形可能限度は異なります。
流路形状は、直線、波形状、S字形状、Y字分岐形状、狭ピッチ流路等の開発実績があります。
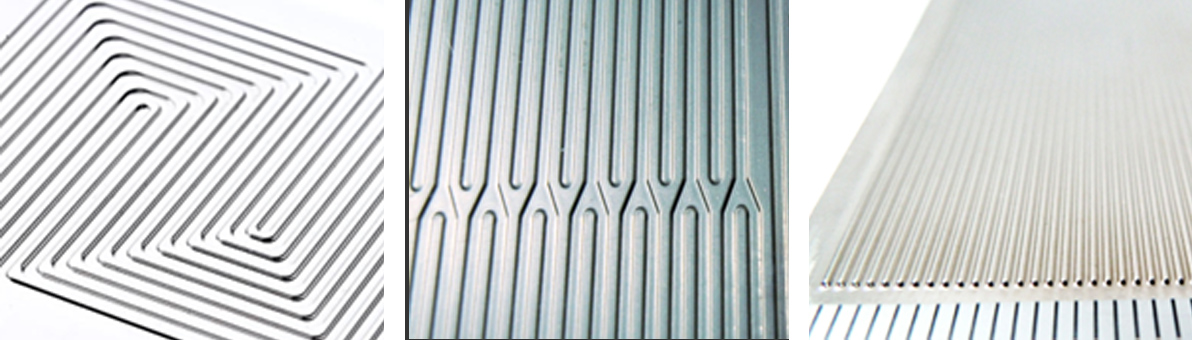
開発内容(サンプルセパレータ)
サンプルセパレータにて形状の異なる3種類の流路を形成しております。お客様のご要望にフレキシブルに対応できる成形技術を持っております。
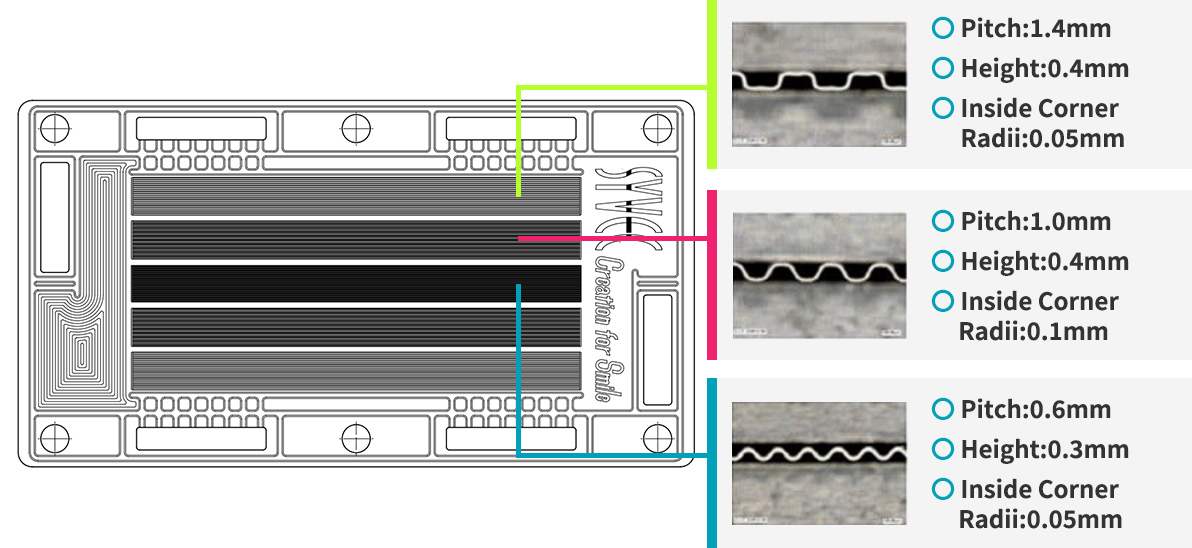
右写真は開発した金属セパレータの流路形状断面になります。
従来のものと比較してプレス加工難易度が高い「流路ピッチ」・「壁角度」・「角R」にて流路形状を設定し開発を行いました。
- 製品材料:チタン、ステンレス t=0.1mm
- 流路ピッチ:2mm(従来の1/2)
- 流路壁角度:2°(従来の1/4)
- 流路角内R:R0.1mm(従来の1/2)
- 流路高さ:0.55mm(板厚含む)
流路断面は均一に材料が伸ばされプレス加工することができました。
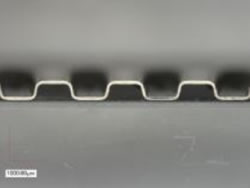
これからの燃料電池の用途
1)産業用燃料電池として利用
工場、公共施設、病院・福祉施設などでは、事業継続計画(BCP)の観点から燃料電池の導入が進められています。
データセンターや公共施設などでは、停電にそなえたバックアップ電源として活用されています。
最近では、工場から排出される二酸化炭素を回収する技術(CO2電解装置)に燃料電池が使われるケースや、水素生成技術(水電解装置)にも燃料電池が使われ、エネルギー脱炭素化に関する技術開発が進められています。
2)バイオガスや水素から発電利用
工場の排水由来や下水処理場から発生するバイオメタンガス、生ゴミなど食品廃棄物由来のバイオガスなどを燃料として発電する燃料電池も導入されています。
3)車両用途として利用
車両の大きさや車体重量、運用環境といった観点から二次電池の採用が不向きなエリアに、バス・トラック、航空機、建機・農機、船舶において、燃料電池の搭載が進むことが期待されています。
今後これらの用途において、燃料電池が「水素社会」のカギとなる重要なものであり、カーボンニュートラル社会に欠かせないデバイスの一つであります。
水素技術で未来を拓く、時代の最前線となる金属セパレータ順送金型の開発
生活者の価値観変化と次世代モビリティの社会実装
近年、生活者の価値観は成長を重視するのではなく、生活の質(QOL:Quality of Life)や自然環境への配慮などを重視するものへと変化してきています。
次世代モビリティは、生活者の移動の利便性を向上させるだけでなく、交通事故の減少や交通渋滞の緩和、環境負荷の低減など、社会全体にもさまざまなメリットをもたらす可能性があります。 今後、デジタルテクノロジーの進化とあいまって、新しいタイプのモビリティが続々と発明・開発され、普及していくことが予想されます。
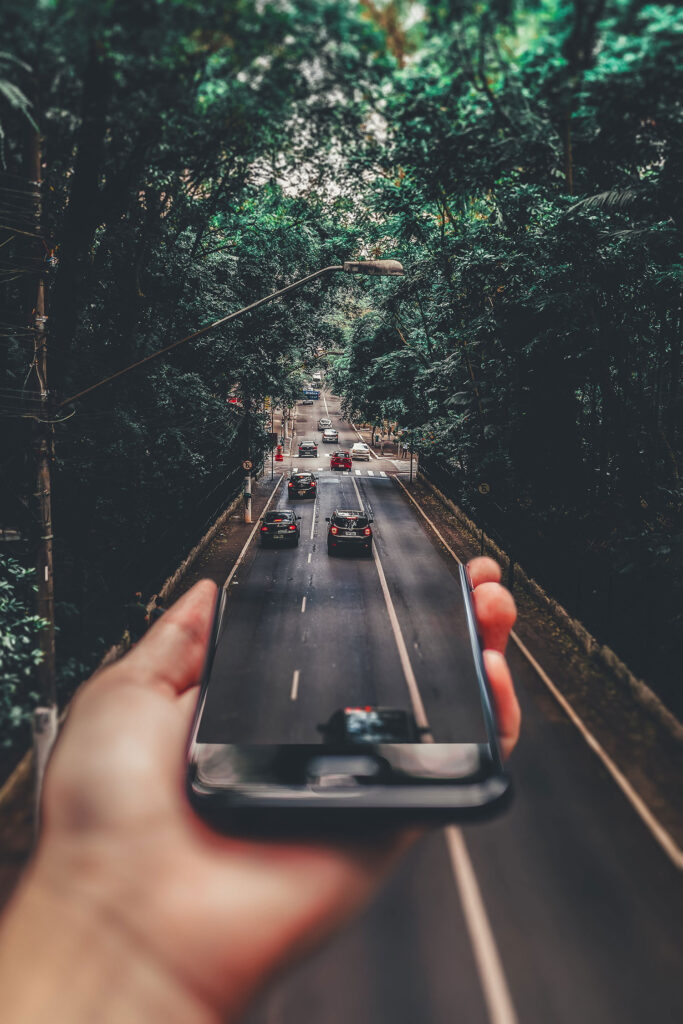
これからのモビリティにおけるギア(歯車)部品の重要性
ギア(歯車)は、自動車の動力伝達や電動化、自動運転、ロボット技術など、さまざまな分野で重要な役割を果たしています。
特に、自動車の電動化と自動運転化が進む中で、ギア(歯車)の役割はますます重要になると期待されています。
また、産業用ロボットでは、精密な動きを実現するために高精度なギア(歯車)が必要となります。このように、ギア(歯車)は私たちの生活を支える基盤技術の一つであり、今後もその重要性がますます高まっていくと考えられます。
インボリュートギアに限らずサイクロイドギア、トロコイドギア等、様々なギア形状に対応できるよう技術開発を行っております。
ギア(歯車)部品の技術開発
ギアの高精度化開発
インボリュートギアの精度等級について
新歯車精度規格(JIS B 1702-1:1998とJIS B 1702-2:1998 )にてN7等級をプレス上がり製品で実現しております。
歯車精度
単一ピッチ誤差 | 14μm相当 |
隣接ピッチ誤差 | 15μm相当 |
累積ピッチ誤差 | 41μm相当 |
歯形誤差 | 15μm相当 |
歯筋誤差 | 18μm相当 |
歯溝の振れ | 32μm相当 |
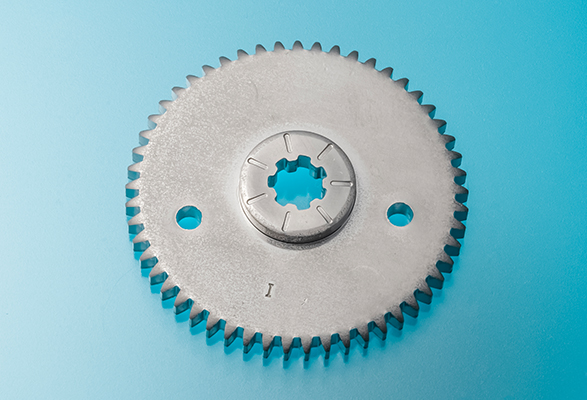
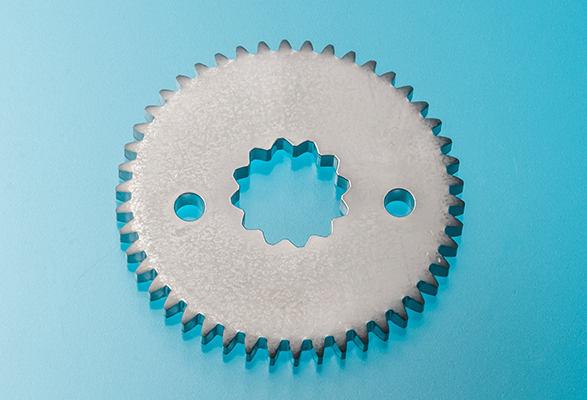
ギアのダレ抑制開発
プレス加工において発生するギアダレに対して技術開発を行っております。
生産性を下げることで課題解決する方法もありますが、順送プレス加工の生産性を維持したまま課題点を解決するプレス加工を目指して技術開発を行っています。
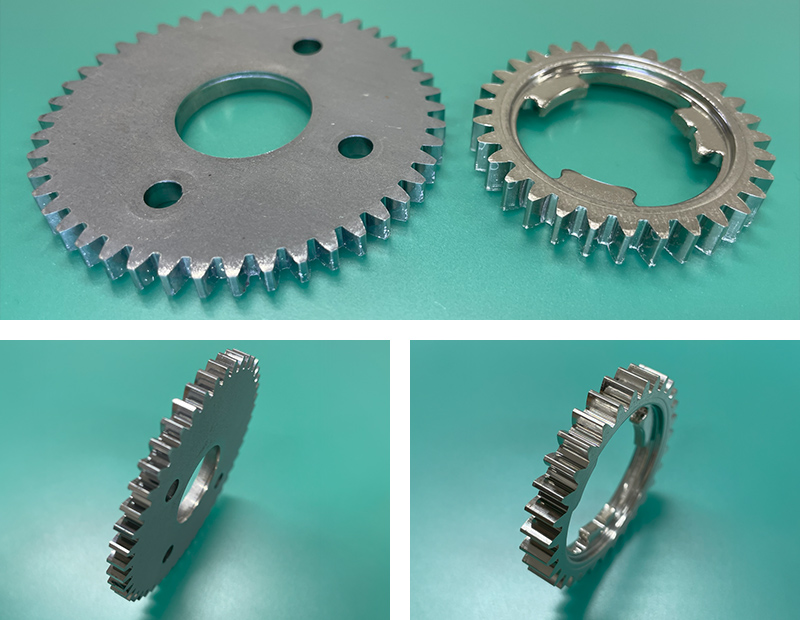
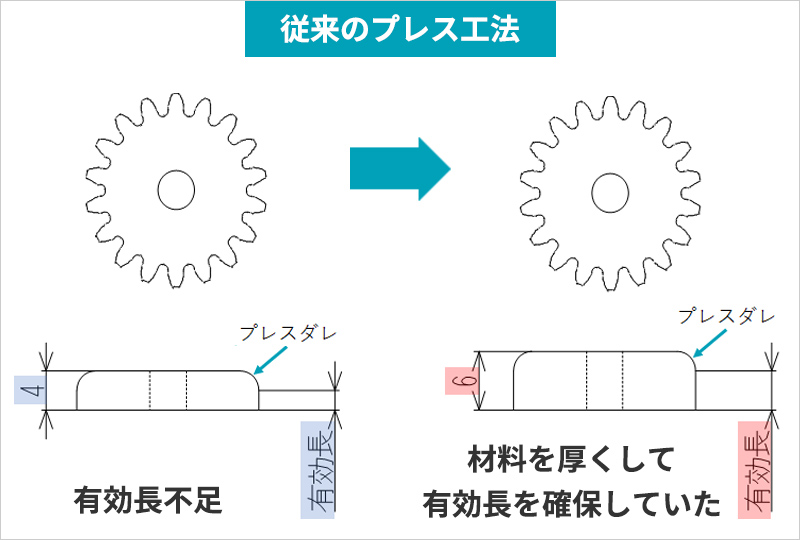
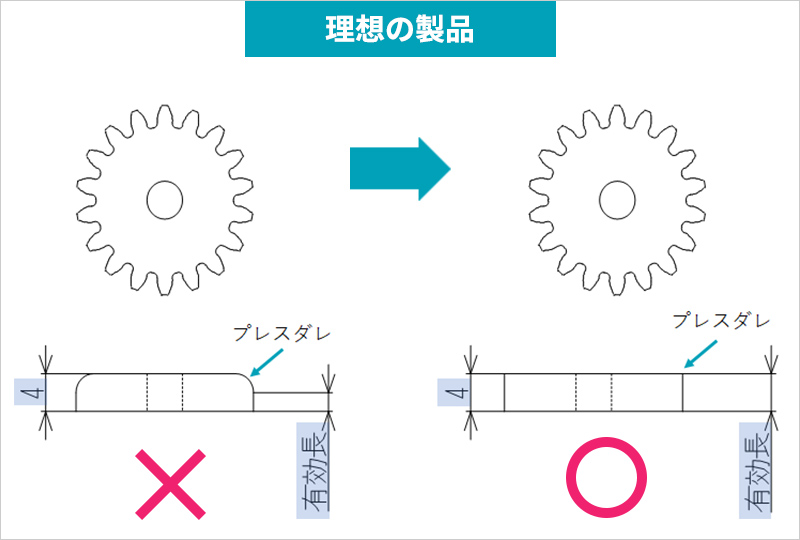
開発中のギアダレ報告
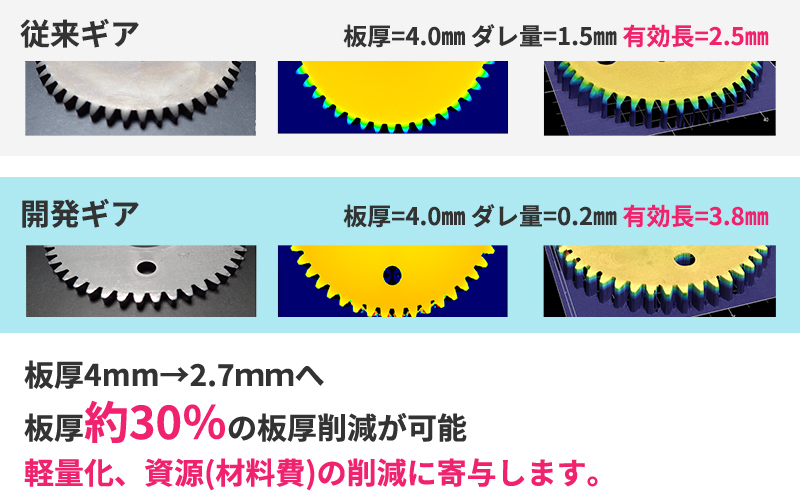
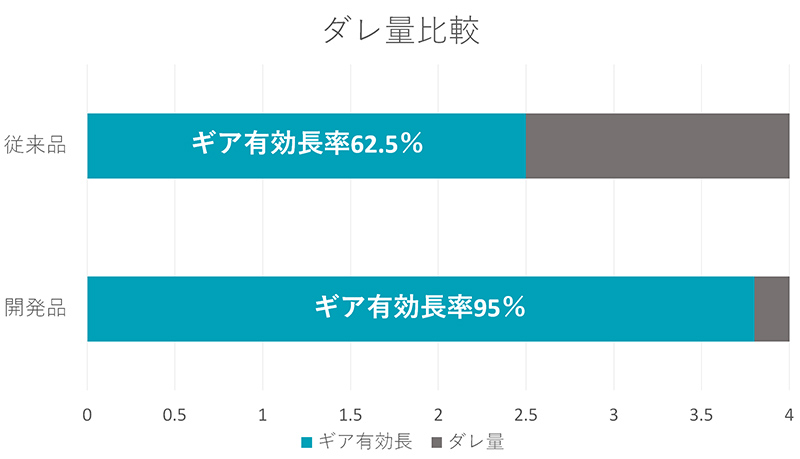