TECHNOLOGY技術・研究開発開発情報
挑戦を続ける、革新を追求する開発
お客様のニーズを第一に考える
サイベックコーポレーションは、プレス加工技術や板鍛造技術を駆使し、金属プレス製品の開発に取り組んでおります。お客様のニーズを最優先に考え、開発の初期段階から要望を深く理解し、技術的な検討を行っております。最適なプレス加工と板鍛造技術を用い、高品質な金属プレス製品をお届けいたします。
最先端の技術を追求する
サイベックコーポレーションは、最先端のプレス加工技術と板鍛造技術を駆使し、金属加工の新たな価値を創造しています。金型製作部門では、機械メーカーと協力し革新技術を開発しており、量産加工部門では、自社開発のプレス機を活用し、高精度・高品質な金属プレス製品を製造しています。常に進化を続け、お客様のニーズに確実にお応えします。
常に挑戦し続ける
サイベックコーポレーションは、プレス加工技術と板鍛造技術を駆使し、常に挑戦を続ける企業です。技術革新が進む金属プレス加工業界で第一線を走り続けるため、新たな技術や製品の開発に積極的に取り組んでいます。私たちは今後も技術革新を推進し、さらなる品質向上と製品開発に注力してまいります。
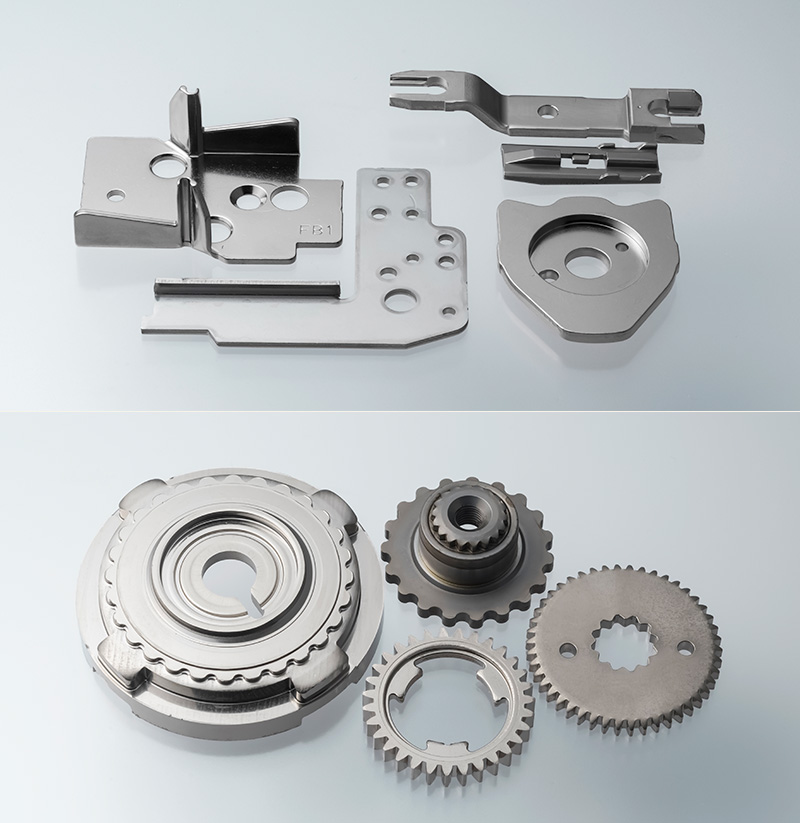