TECHNOLOGY技術・研究開発CFP技術とは
サイベックコーポレーションのCFP工法とは?
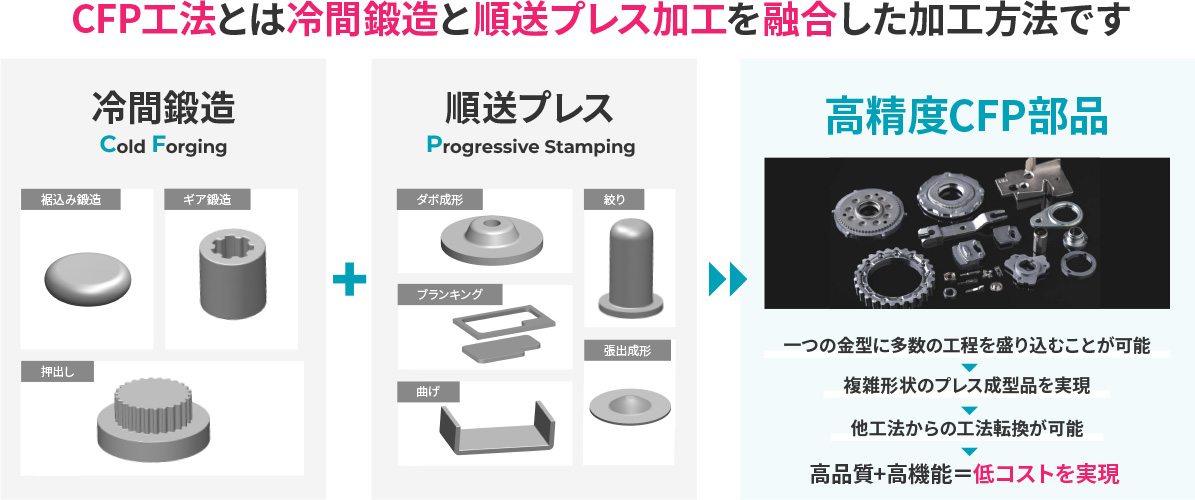
サイベックコーポレーションのCFP(Cold Forging Progressive)工法は、板材から複雑な形状の部品を、高強度・高精度で量産できる革新的な鍛造技術です。
従来の鍛造技術では、複雑な形状の部品は、切削や研削などの加工を組み合わせて製造する必要がありました。そのため、コストが高く、精度や生産性に課題がありました。
CFPは、冷間鍛造と順送プレス加工を組み合わせることで、これらの課題を解決しました。
冷間鍛造により、板材を高強度に鍛造し、順送プレス加工により、複雑な形状の部品を高精度に成形することができます。
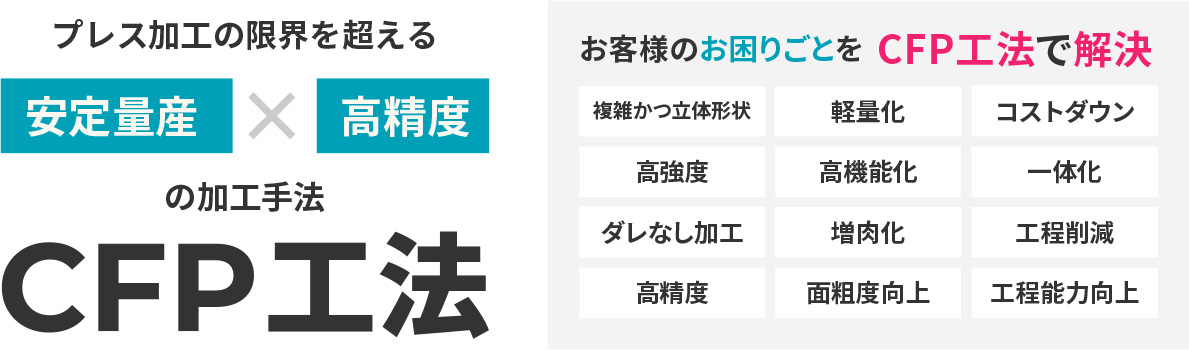
CFP工法のメリットや特徴
- お客様の開発段階である「焼結+機械加工」「プレス+機械加工」「切削」「研削」といった加工を、CFP工法にて大幅なコストダウンを実現します。
- CFP工法は金型部品精度をミクロンオーダー1μm以下で管理している為、量産部品の形状や寸法をより安定的に生産することができます。
- CFP金型の開発から設計→金型製作→生産→品質保証まで行いますので、ご要望に応じた柔軟な対応が可能です。
- CFP工法は板材から複雑な立体形状部品をハイスピードに量産するため大幅な加工能力UPとコストダウンを実現します。
- お客様の期待や想いをプレス品としてお届けするために、スピードある開発体制(VT研究所)を整備しております。
CFP工法のターゲット
従来他工法で製造していた部品をCFP工法へ転換をすることにより、コストダウンが可能となります。
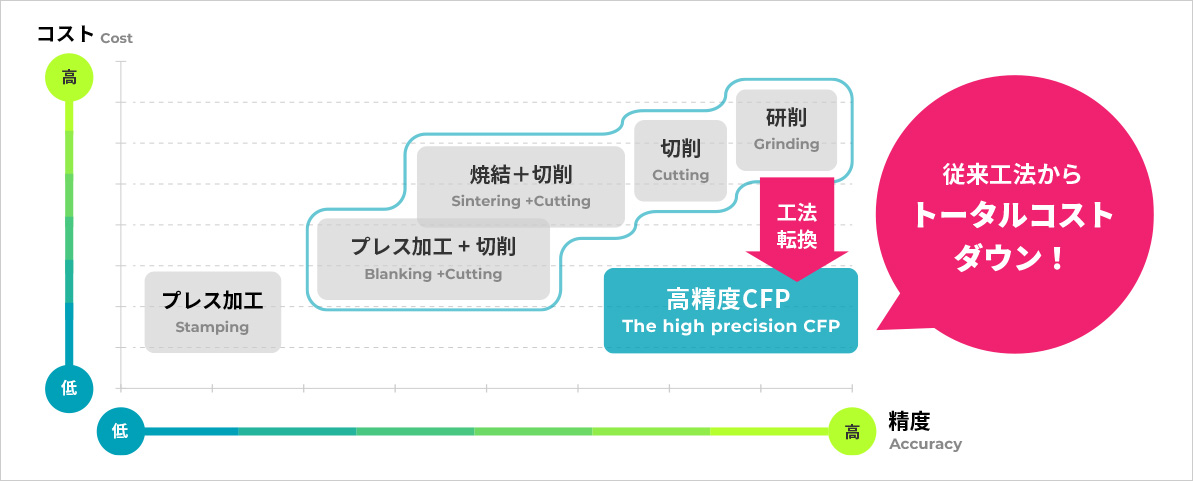